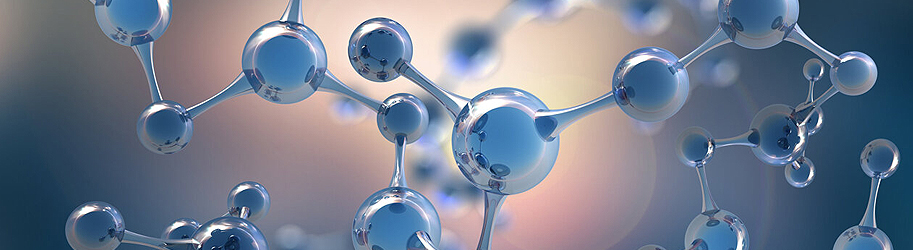
POLYMER TECHNICAL DICTIONARY
Flow rate
The Melt Flow Index (MFI) is the amount of polymer that flows in the melt through a standard nozzle (2,0955 x 8 mm) at a given temperature, under the weight of standard masses that press on a piston. Basically, it is a measure of the flow rate of the polymer melt, and indirectly, its viscosity and molecular weight. The flow index is measured according to ISO 1133 or ASTM 1238. The polymer flow can be measured mass (ISO 1133-A / MFR – Melt Flow Rate, expressed in g / 10 min) or volumetric (ISO 1133-B / MVR – Melt Volumetric Rate, expressed in cmc / 10 min). Method B is useful for filler polymers. The temperature and reference weights of the test masses are chosen according to the polymer tested in order to best characterize its rheological properties.
The most common specific test conditions are (ISO 1133):
The most common specific test conditions are (ISO 1133):
Polymer | Temp / Mass |
Polyethylene | 190 ºC / 2,16 Kg 190 ºC / 5,00 Kg 190 ºC / 21,6 Kg |
Polypropylene | 230 ºC / 2,16 Kg |
Polystyrene | 200 ºC / 5,00 Kg |
ABS | 220 ºC / 10,0 Kg |
Polycarbonate | 300 ºC / 1,20 Kg |
POM | 190 ºC / 2,16 Kg |
PMMA | 230 ºC / 3,80 Kg |
Flexural modulus
The bending modulus (bending strength) represents the bending force of the material in relation to the elongation under load. It is practically a measure of the rigidity of the material, of its resistance to deformation. The higher the flexural modulus of a material, the more rigid it is. The SI unit of measurement is Pa (N / m2). In the field of plastics, the usual values are of the order of megapascals (MPa = N / mm2) or gigapascals.
Typical values of the flexural modulus:
Typical values of the flexural modulus:
Material | Flexural Modulus [Mpa] |
ABS | 2.500 |
ABS + 30% GF | 7.000 |
Acetal Copolime | 2.500 |
Acetal Copolimer + 30% GF | 7.500 |
PA 6 | 2.300 |
PC | 2.300 |
PE | 700 |
PET | 1.000 |
PP | 1.500 |
GPPS | 2.500 |
Contraction
The contraction of the polymers is due to the change in their volume during the transition from the melt to the solid phase, and subsequently the cooling in this phase, and is expressed as a percentage, as a variation of the volume (shrinkage index). In the molten state, all polymers have a random distribution of macromolecules. Below the vitrifying temperature (Tg), however, crystalline polymers (actually – semicrystalline) tend to arrange macromolecules, so that crystalline polymers will have a more significant reduction in volume in the solid state than amorphous ones, and thus a shrinkage index. bigger. In general, the density of semicrystalline polymers in the melt is about 80% of the density in the solid state, while that of amorphous ones is about 90%.
Also, a polymer with a higher molecular weight will have a higher tendency for the macromolecule to relax after the stress it is subjected to during the injection, leading to a higher shrinkage, and generally differentiated in the direction of flow from that. transversal. Copolymers and filler polymers generally have lower shrinkage rates.
Typical values of contraction indices:
Also, a polymer with a higher molecular weight will have a higher tendency for the macromolecule to relax after the stress it is subjected to during the injection, leading to a higher shrinkage, and generally differentiated in the direction of flow from that. transversal. Copolymers and filler polymers generally have lower shrinkage rates.
Typical values of contraction indices:
Material | Type | Degree of crystallinity | Shrinkage index |
HDPE | Semi-crystalline | 70 – 80 | 2 – 6 |
LDPE | Semi-crystalline | 45 – 55 | |
Polypropylene | Semi-crystalline | 70 – 80 | 1 – 2,5 |
Polypropylene 40% GF | Semi-crystalline | 0,2 – 0,8 | |
PA 6 | Semi-crystalline | 0,5 – 1,5 | |
PA 6.6 | Semi-crystalline | 35 – 45 | 0,8 – 1,5 |
POM | Semi-crystalline | 70 – 80 | 2 – 2,5 |
PEEK | Semi-crystalline | 0,7 – 1,9 | |
ABS | Amorphous | 0,4 – 0,9 | |
PC | Amorphous | 0,5 – 0,7 | |
PS | Amorphous | 0,4 – 0,7 | |
PMMA | 0,1 – 0,4 |
RoHS
RoHS (Restriction of Hazardous Substances) is a European standard (CE / 2002/95) restricting the use of certain hazardous substances in electrical and electronic equipment. RoHS seeks to reduce the amount of hazardous materials entering electronic products and is closely related to the EC / 2002/96 Directive on waste electrical and electronic equipment (WEEE).
Annex II contains the list of restricted substances:
Annex II contains the list of restricted substances:
Substance | Acronym | Conc max(MCV) |
LED | Pb | <1000 ppm |
Mercury | Hg | <100 ppm |
Cadmium | Cd | <100 ppm |
Hexavalent chromium | Cr (VI) | <1000 ppm |
Polybrominated biphenyls | PBB | <1000 ppm |
Polybrominated diphenyl ethers | PBDE | <1000 ppm |
Di (2-ethylhexyl) phthalate | DEHP [Ro: DOF] | <1000 ppm |
Benzyl butylphthalate | BBP | <1000 ppm |
Dibutylphthalate | DBP [Ro: DBF] | <1000 ppm |
Diisobutylphthalate | DIBP [Ro: DIBF] | <1000 ppm |
The RoHS list remains open, depending on future proposals and other substances will be included, while there are some exceptions where these substances cannot be replaced efficiently, such as: mercury in many types of fluorescent lamps. , lead in steel and aluminum alloys, lead in some types of soldering and military applications.
The editions published so far are:
The editions published so far are:
Edition | EU standard | Remarks | |
1 | RoHS | CE/2002/95 | Restrict the first six substances in the list. |
2 | RoHS 2 | CE/2011/65 | Enter the CE marking of the products. |
3 | RoHS 3 | CE/2015/863 | Add phthalates to the list of restricted substances. |